On my Viggen That plastic crap had to go. The early cars had a nice aluminum piece, didn’t have the right sensor ports. Sorted that and all we got was a burst of Spark knock pulling away from a stop in the heat.
The one good thing about having your own OEM level chassis Dyno for R&D in house is the Truth It didn’t make a bit of power.
So I thought it we made a stainless one it would help Heat rejection. If it was a bit larger surely that would help. This is where it got interesting. It made nice gains on our 2.0 T5 hotrod. Not on the Viggen.
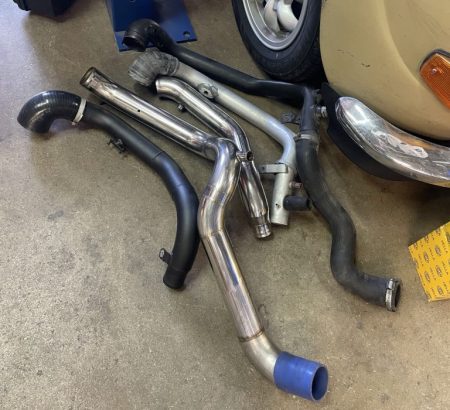
Got with Adam and we made a 2.5” stainless that went all the way to the intercooler. In this case an upgraded KylarJohnson from Sweden or the larger and better cooling ETS made here in the states on the 2.0.
No gains, the heat issues got worse.
By then the power was a nice 500 at the tire. The pressure drop was great at 2.5psi compressor to manifold at peak. Compared to the sub 1psi on our 700whp drag car!
One was a compromise. A 2-1/4” aluminum. Machined a tidy sensor mount and tucked in in nicely. Gentle transition cone too. Powder coated it in a texture black to match the stock stuff.
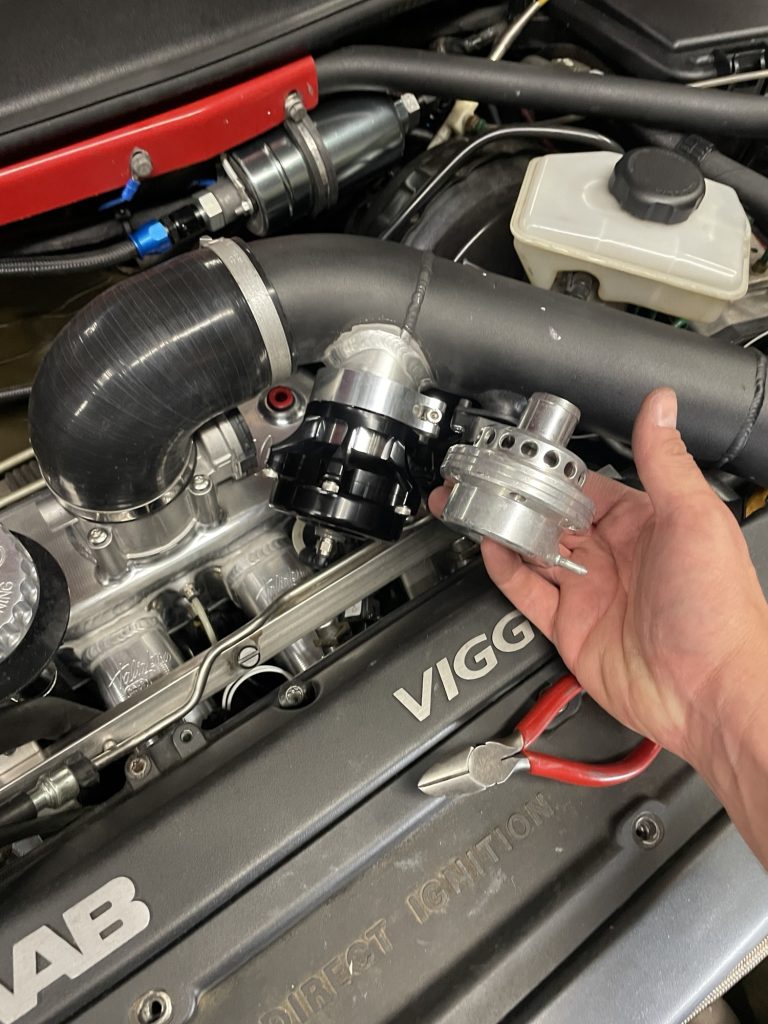
In the spirit of the original TURBOs I made a few badges, not sure on the placement.
Now wait, what’s that fat 2-3/4 with the big Tial 50mm blowoff? I finally Found the problem!! The main difference between T5 and T7 is the Throttle…. And why the bigger pipe was only a problem on the T7 cars. It doesn’t help anything. Looks pretty though.
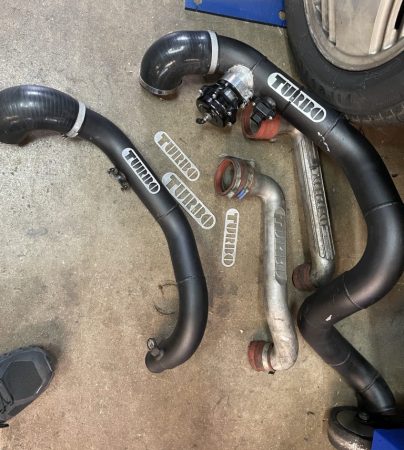
If you look. Closer in the above iteration of the Viggen. Its 52mm Stock throttle has been replaced with a 68mm Realizing Huge gains on the Dyno. More on this in the next post.