So you are putting a quaife in your gearbox, maybe you broke it and want to build it stronger.. Well here we will start on some of the tricks.
First some education, had to start somewhere..
F25, F35 F40 what does that mean? The F25 is a type designation for the gearboxes fitted to the NG900 94-02. They are rod shifted. There were a few different versions of that box also. More on that later.
F35 this is the version with cable shift fitted to the new 9-3 and Cobalt SS/ HHR. But then you ask why does the Viggen and 9-5 use a F35 differential but still a rod shifter. They are simply F25 with the larger diff splines of the F35. The 9-5 has a larger heavier flywheel so it gets a deeper bell-housing. All the internals are the same. Just part of the case.
F40 is the 6 speed in the new 9-3. It is a very robust gearbox with TWO output pinion shafts! this is part of the reason they are quite noisy and clunky. It only in the new ecotec bolt pattern. If you can find one of the super rare euro diesel 6 versions it will bolt up to the B2x5/4 engines.
6speed Quaife F25/35 Gearset
There is nothing Saab specific here. The kit was developed to fit the Cobalt SS and similar F35 cars. it just happens to fit in the F25 cases also. For the NG900/9-3 and 9-5 it is a straight swap. For the 9000 94-98 since the trans mount is part of the end case that is changed you have to fabricate a new mount assembly. This is just the gearset and you need to have some extra parts from Saab to make it all work. The final drive can be selected from the few that we have from 4.05 std in 9-3/9-5, 4.45 and 3.82 so you can move the gearing around. You will need to have the ring and pinion as a set. Not the easiest to swap but still an option.
The biggest reason to run the new gearset is the higher first and closer rest of the gears 6th is acutally about the same as the higher geared 9-3s.
So what breaks them? Wheel hop is the worst killer. The shock load when the tires bite tears stuff up. Same goes for burnouts. Another killer is just simply massive torque overload but that takes lots more power. You know the gearbox really doesn’t care about horsepower right? It only matters how much torque it transmits. How can that be.. HP is only torque by RPM so the more high rpm torque you make above 5250rpm you will make more HP.. Sometimes the crush sleeves collapse releasing some of the bearing preload and this reduces shaft stiffness leading to carnage. The differential is not such a fan of big torque or wheelspin either. Usually when it fails you ventilate the case. Other times the cause is pure abuse..
So you just what to know what to do to the box to make it last. When installing the quiafe it is pretty simple. Use the right new parts, set the bearing preload just perfect and treat it right.
If you have a 9-3 or 9-5 in the following range and any of the following issues: Blocked 2nd gear, Blocked reverse gear, Difficult to engage 3rd-4th gears, Difficult to engage 5th gear, or Difficult to disengage 3rd-5th. Saab even says to update if for any reason you are inside.
o MY99 – MY01 9-3 up to and including VIN 12029080
o MY99 – MY01 9-3 Convertible up to and including VIN 17007508
o MY99 – MY01 9-5 up to and including 13025469
The update kit changes a bunch of parts inside and also gives you some of the one-time items that have to be replaced when you open the gearbox.
Crush Sleeve
One thing that is not in the upgrade kit that should be in every high output gearbox is the new crush sleeve from the F35. This was even used in the -03 9-3CV with the F25.
Interestingly the new crush sleeve has not come in any of the kits. It has not been superseded but you can and should use the updated part in the older gearboxes as a minimum.
For the next step past level 2 you can machine and parallel grind steel spacers to take the place of the crush sleeve but care must be taken to get just the right thickness for proper preload. This either takes an assortment of shims or the ability to surface grind custom to the application. This can be quite time consuming since you have to chase it and then tear the case back apart to change the shims. With stock crush parts you just squeeze it till the numbers are right.
Article : Sleeve (Old, Barrel with spacer)
PartNo : 8734477
Usage : 1998-2002
Article : Sleeve (New, Ridged cone)
PartNo : 55352125
Usage : 2003-,
Here you can see both. Interestingly most of the old barrel spacers crack around the equator from fatigue.
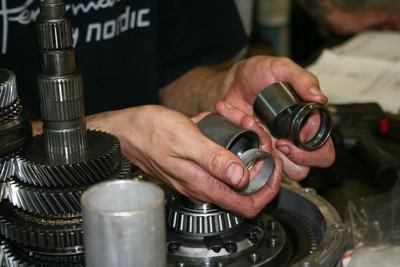
So why should I care about this spacer?
Well in the gearbox it is the taper roller bearings that support the shafts. You need enough preload to keep the shafts rigid, that is not allow them to flex in the middle to keep the gears tight. Since the aluminum case expands more than the shafts you also need a little tension when cold so that is is still tight when the gearbox is hot. But also you can have it too tight and hurt the bearings with cold use if it is too tight and make too much heat on extended use. Normally on the high output T7 cars I setup the cold rev limiter a little lower that 5k just so that the gearbox has some chance to warm before seeing high speeds. The high load when cold is something that the driver just has to care about.
}–\/–{
}–/\–{
Tab Bolt
The steel sheet Brace / bracket that holds in the pinion bearing also runs over the diff to reinforce the case. The problem is that it simply has a screw in an oversized hole to clamp it down. Under repeated hard loadings (And thermal cycles due to varying expansion rates of the Steel and Aluminum) the tab actually scoots under the bold fretting and wearing the alu case away loosing effectiveness. The solution for this is to machine it to hold a special dowel pin bolt that fits tight in a reamed hole so that the pin takes the shear load and the bolt threads only hold the clamping tension. You need to open the hole up to 10.00mm This does take a vertical milling machine and some care in the setup to get the new reamed hole concentric with the original threads. The hole must be drilled close and reamed to final fit. The threads much be cleaned up since the drill usually pushes a burr down. This mod takes about 30 min and should be done on all "level 2" gearboxes. Gallery Link
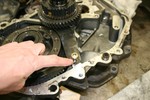
Extra Dowels / Case bolts
The extra holes with no hollow dowels should be filled with new dowels so that maximum reinforcement is possible between the two case halves. Also as Saab fitted to the later gearboxes better case bolts especially around the diff help quite a bit.
..continued
Trans fluid is a compromise between lubricating the bearings and gears while still providing enough friction that the synchronizers will function properly to match the gear speeds. Then there is the stiction that causes detent and syncro problems like the early 9-3 boxes.
So you can see that the oil will not be able to "fix" a crunchy syncro…
The few gearboxes I have taken apart that came with the blue/green MTL had very odd looking syncro’s, they were polished. One about a week after change on a low mileage viggen jammed Reverse syncro ring it would not come off the gear.
There are a few different trans fluid groups that have different combinations of these properties. I stick to the factory 0063 and just work to keep the trans temp within the limits of the fluid. Since after all it is not generally a bearing failure that kills our gearboxes but rather massive overload failures.
Having a couple 500hp one with 500ftlb the first box broke with 400tq.. and no drag strip. New one has a nastier clutch and more 1/4miles than I care to think about. With 8.5" Slicks there is no wheelspin.
Wheel-hop is the primary killer, after that spinning wheels and the associated tq spike when it bites. Has nothing to do with power delivery. You get 10x the spike when shifting hard running too much clutch Put it on a dyno and run it from 3rd to 4th in road mode while logging the tq. ouch. Sure will teach you to shift better after seeing that data. Also you want to run enough clutch to hold the power without being overly aggressive and the resulting shock loads.
Reuse the ring gear bolts? I use ARP bolts for all the ring gears. Cheaper than factory. I have reused the ring gear bolts a single time on low output cars. It is cheap insurance to replace.
Minimum parts to install a Quaife?
Quaife depends on app
Differential bearings 2x 12788353 ($39.45 ea)
Crush sleeve 55352125 ($58.05)
Locknut, Pinion 12755195 ($9.56)
Gasket kit 8781494 ($82.00)
MTF-0063 2x 93165290 ($10.50 ea)
ARP Ring Gear bolts Set of 12 KIT ($64.00 kit)
Shims As required (various numbers.)
Update Kit 5440516 ($237) LINK
(Prices Feb 2009 MSRP our price -15%, all these parts are stocked even though they may not be in the catalog.)
There are quite a few special tools required to keep you from chipping 5th gear or aid in calculating preload for example. I would leave gearbox rebuilding to someone that has done quite a few of these gearbox especially if you are running a high output car where the margin for error has been reduced with high loads. How long? Well depends on the car and the technician. Around 10 hours is quite reasonable. If there are more updates than just a diff count on a bit more time.
Some of my upgrades can only be done if you have access to a machine shop. Pinning the pinion brace, using a spacer instead of the crush sleeve etc.
No reproduction permitted
Nick Taliaferro 2009 Any questions just email me.
What do I have to do to use a viggen transmission into my 97 900se?
Well the biggest hurdle will be the driveshafts. The Viggen uses the F35 differential and the splines are not the same. So the quick answer is to get Viggen driveshafts right, partially. The Viggen also used the larger 9-5 outer CV joints. They have a larger diameter ABS ring too and will not clear the normal uprights. You could get the Vig ABS sensor mounts and have a local machine shop clearance the upright for the cv joint. Not sure how reasonable this is but probably the only easy option. Otherwise you can put a F25 diff inside with a gearbox rebuild and it will drop right in.
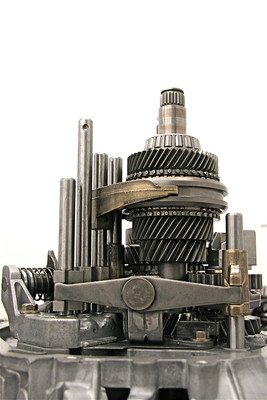
For more gear ratios etc look in the gearbox pics Gallery